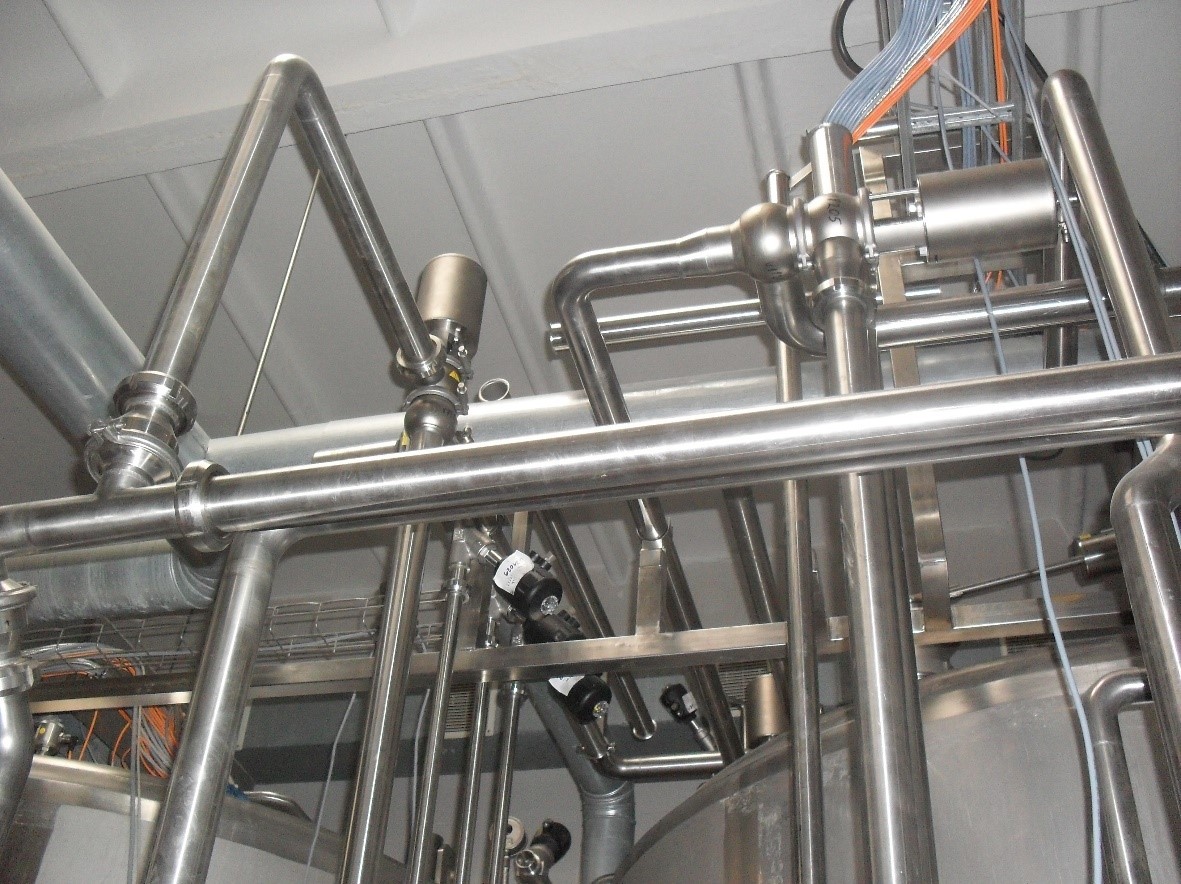
Installation of pipelines
We make installation and piping of the process equipment by pipelines made of stainless steels AISI-304L, AISI-308L, AISI-316L, AISI-321, st.20-30, titanium and aluminum, widely used for chemical, food and pharmaceutical industries for various process media:
Water, compressed air, CO2, technical steam, food steam, sulfuric acid, argon, oxygen, propylene glycol, gaseous and liquid freon, milk and milk products, micro-sensitive liquids and chemical solutions.
At pipelines installation facilities we use the following thicknesses of the walls of pipelines and shaped products:
In order to meet the requirements for rolled metal products, pipes, shaped products of pipelines, piping components, shut-off and regulating devices, sensors, flowmeters, we are able to complete large and small projects at competitive prices.
For installation work, the following are used:
- Manual argon-arc welding (WIG-TIG), pipe diameter from 6 mm, wall thickness – from 0,8mm;
- Orbital welding (WIG – TIG), pipe diameters from 20mm to 115mm, wall thickness – up to 3mm.
When installing pipelines we use various technologies for welding process:
- On the pipeline walls up to 2,6 mm – (AISI – 304L, AISI -316L – AISI – 321) – application of Pendel- method without application of filler material. Method WIG-TIG.
- Pipe walls more than 2,6 mm – welding with edge cutting and application of filler material – Pendel (WIG-TIG).
- Walls of pipes more than 8 mm- welding with edge cutting and filling of intermediate layers by MMA or MIG-MAG method.
The undoubted advantage of the combination of manual argon arc and orbital welding is the opportunity to gain an advantage both in quality and speed, and in pricing.
Assembly, welding, as well as all related activities are performed by highly qualified personnel of our company.
In the course of the work, modern welding equipment is used by the firms “EWM”, “Orbitec”, etc.
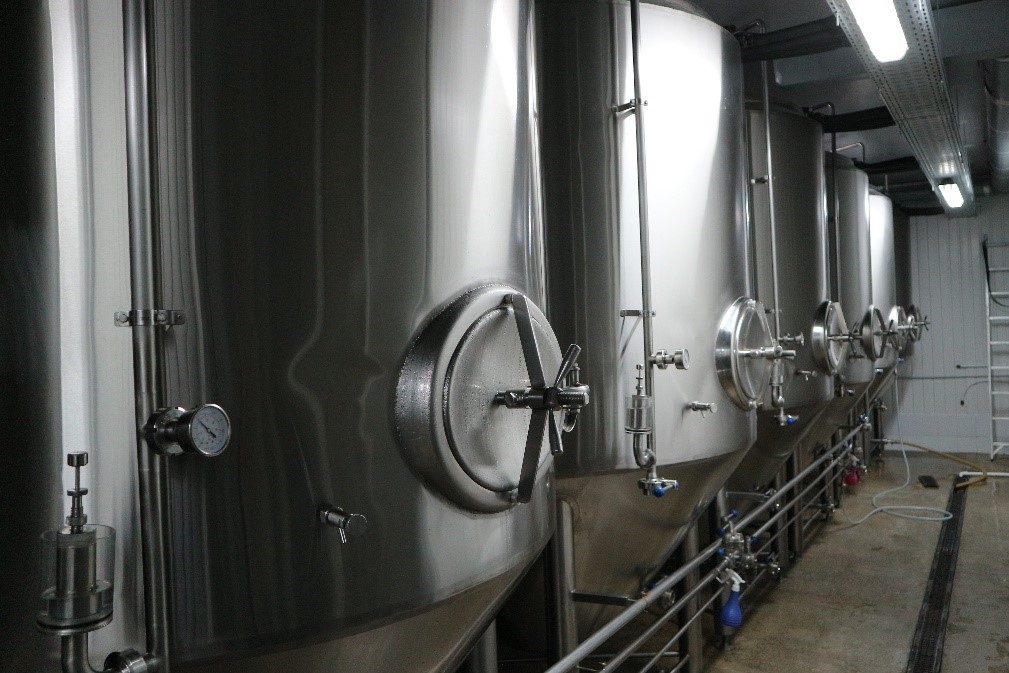
Manufacture of the capacitive equipment
Throughout the company’s activity, we produce containers of various volumes, from various materials, for different environments: Water, propylene glycol, milk products, bulk substances, alcohol, beer, acid, alkali, oil products, gases, compressed air.
Capacity of the volume up to 5 – 7 m3 – we manufacture at our production site.
The volume of more than 8 m3 – we produce the manufacture of individual units and segments in our shop, then mount it on the customer’s site.
We manufacture containers of non-standard shapes and sizes – when there is a need to install the product in a limited space with a non-standard configuration.
Stirring devices can be installed on the vessels or cooling-heating shirts are provided. Two versions of the coolant are liquid or electricity.
Materials used:
- High-alloy steels: AISI-304L, AISI-308L, AISI-316L, AISI-321
- Non-carbon steel: St.10, 20, 30.
- Aluminum and its alloys: AL, AMG, AMC.
- Titanium: ВТ1-00, ВТ-0
For the manufacture of capacitive equipment, argon-arc and semi-automatic welding in shielding gases
WIG – TIG, MIG – MAG
Go to the photo of the manufacture of the capacitive equipment>>>
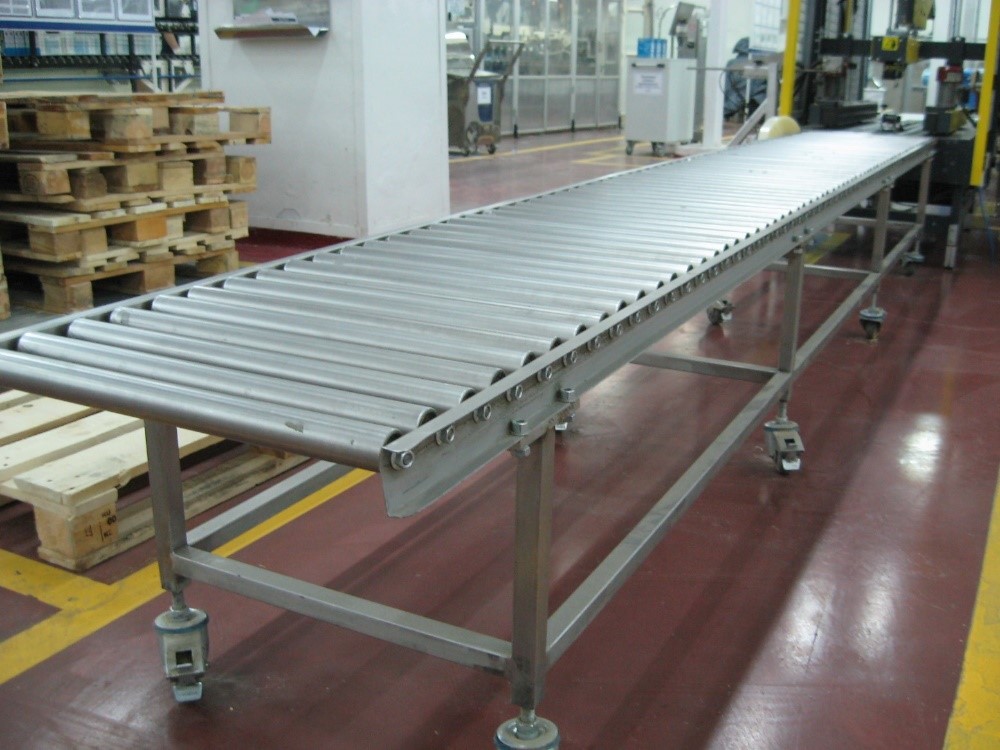
Equipment for industry
We manufacture additional equipment for operating mechanisms, blocks, existing lines, which are structural elements of food and chemical industries.
We also manufacture and maintain the following types of equipment:
- Conveyors and roller tables (rotary and lifting types, by the type of belts: endless, modular, scraper);
- Transitional bridges;
- Baths for washing;
- Bunkers for bulk products;
- Bathrooms for receiving, loading, unloading the product.
In the course of work, turning-milling processing is used, as well as modern welding technology for working with high-alloy, low-carbon steels, aluminum and titanium.
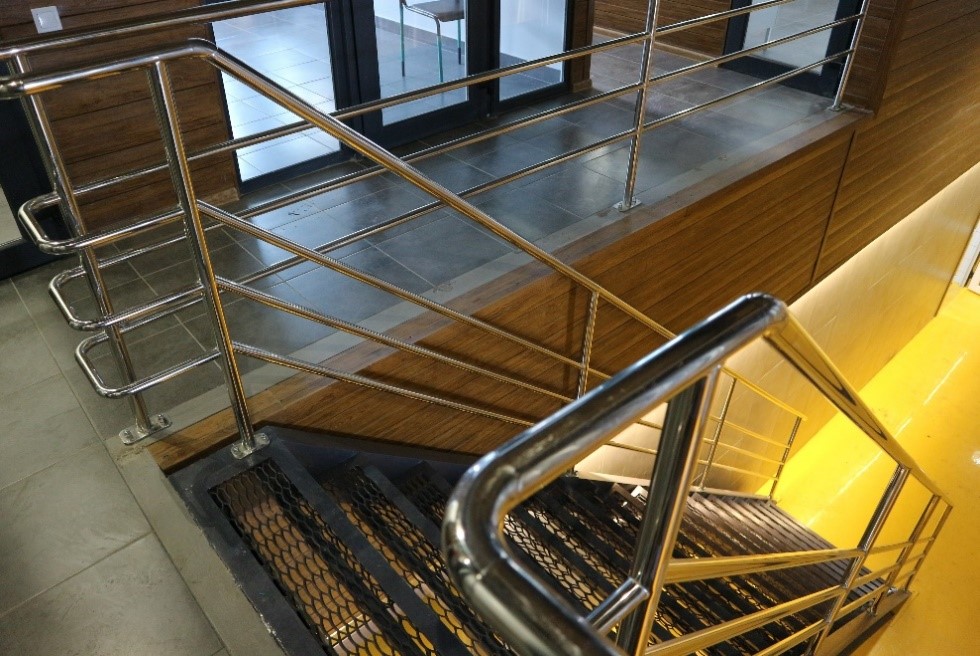
Metal structures and service areas made of high-alloy steels, aluminum, St.20:
During the installation of process equipment, vessels, pipelines, valve groups, cable routes, installation of pneumatic and electrical communications, control cabinets – there is a need for the development of fasteners, auxiliary structures and service areas.
For 11 years of existence the company LLC “VRS Group” – the team has gained extensive experience in the development, manufacture and installation of auxiliary structures and service areas at the enterprises of customers.
Metal structures and service areas are divided into four categories:
- Manufactured from St.20 (“black steel”) – this kind of structures and sites can be painted with chemically resistant enamels or powder paint. Application both outside and indoors. Manufacturing technology implies the use of: WIG – TIG, MIG – MAG welding.
- Constructions from aluminum and its alloys – such designs are rarely used, in cases where the Customer wants to have a strong, light and mobile (mobile) platform or support system for the convenience of his staff. For the production of WIG – TIG (AC), MIG MAG – welding.
- Constructions, trusses, fastening elements of pipelines, ladders, frames for mounting control cabinets, many and one-level maintenance platforms – made of high-alloy steels (stainless steel) – are used most often. Strength characteristics, corrosion resistance, elegant appearance – make high-alloy steel (AISI-316L, AISI-304L, AISI-430) most applicable for most structures working in chemical and food industries.
- We have experience in manufacturing interior design for offices, banks, shopping complexes.
We manufacture and manufacture structures from high-alloy steels (AISI-304, AISI-308, AISI-316, AISI-321), st.20, aluminum, brass.
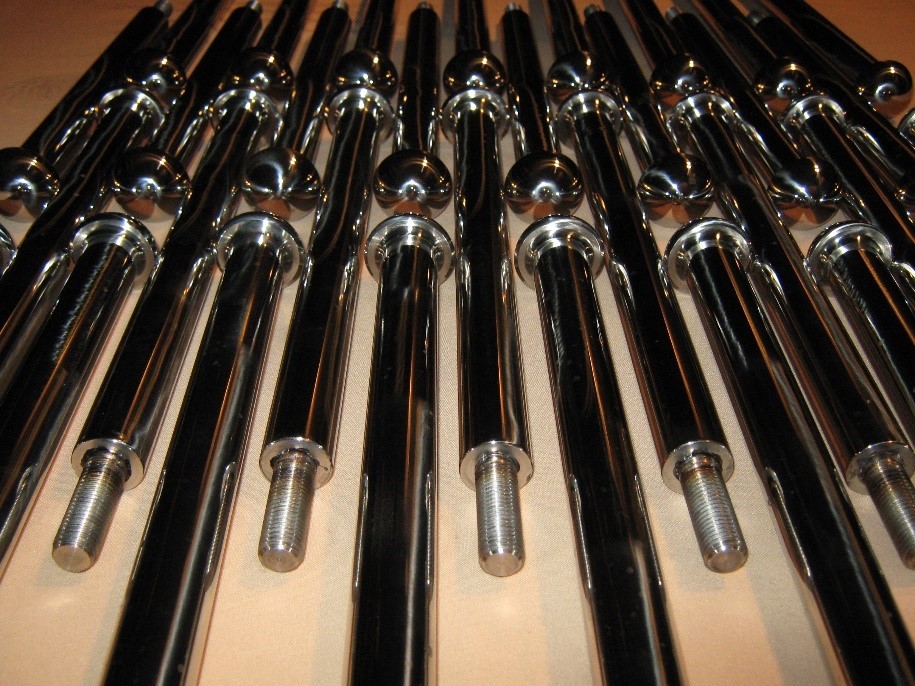
Serial production
At the request of the customer we will develop and provide a combination of metal construction with wood, glass, composite materials.
We provide services to produce serial welding products
We offer complete solutions to produce serial products from metals in accordance with the stages of the preparation of production cycles: marking, cutting, deburring, rolling, assembly of products for potholders, welding, passivation, packaging.
Examples of serial work: stainless steel hooks, sheet metal gratings, round bars, shell structures, welding of pipe elements, etc.
Materials used: low- and medium-carbon, medium-high-alloy steels, aluminum.
For the production of serial welding products, we use: WIG – TIG Hand, WIG – TIG Orbital, MIG – MAG, contact welding.
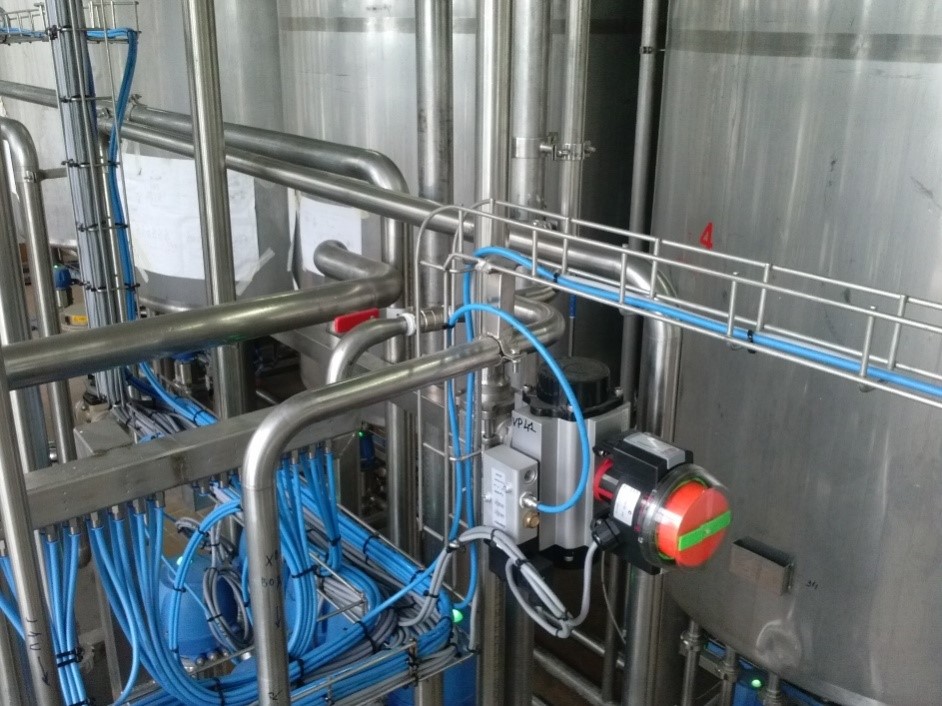
Electrics and pneumatics
We also perform works on electrical installation and pneumatics:
- Installation of cable routes (cable trays – stainless – galvanized)
- Installation of power cabinets
- Installation of control cabinets
- Laying of power cables and control communications (“weak point”)
- Connection of power cabinets and control systems
- Connection of electric motors
- Installation and connection of sensors, valves and process control systems
- Installation of pneumatic control systems for valves and valve groups
- Commissioning works on testing, testing and commissioning of mounted equipment and control systems for the workshop, plant